Top 5 Die Problems in Furniture Hardware Stamping for Sofa Legs
Release time:
2025-03-19
Common Problems with Furniture Hardware Stamping Dies for Sofa Legs
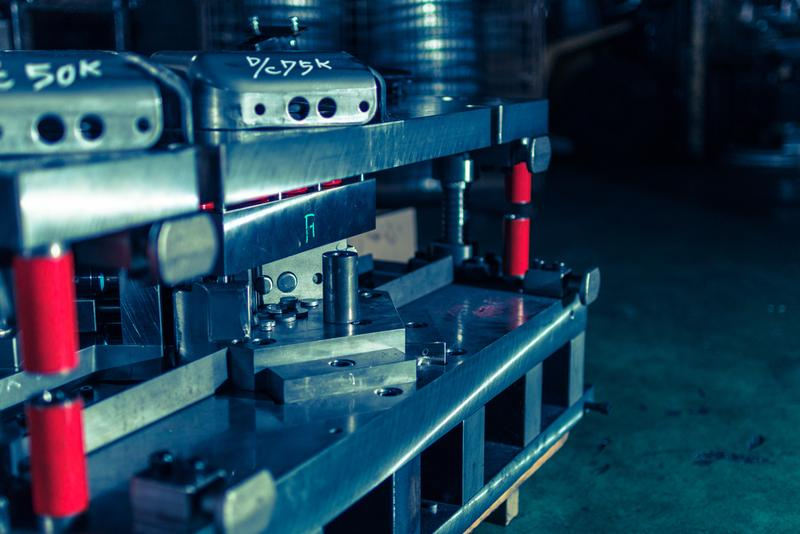
Punch presses are essential stamping pressure machines in sofa leg production. In our factory, the stamping process offers significant advantages over traditional machining methods, including higher material utilization rates, stable production efficiency, and strong automation compatibility. Additionally, it requires minimal operator skills while achieving product features impossible with standard machining. These benefits have made furniture hardware stamping increasingly widespread in manufacturing.
Critical Impact on Furniture Quality and Safety
As key load-bearing components in sofa support structures, the stamping quality of sofa leg hardware directly affects both furniture safety and longevity. During continuous stamping processes for furniture hardware components, convex die wear presents the primary challenge affecting die lifespan. This manifests in several specific ways:
Five Common Furniture Hardware Stamping Problems and Solutions
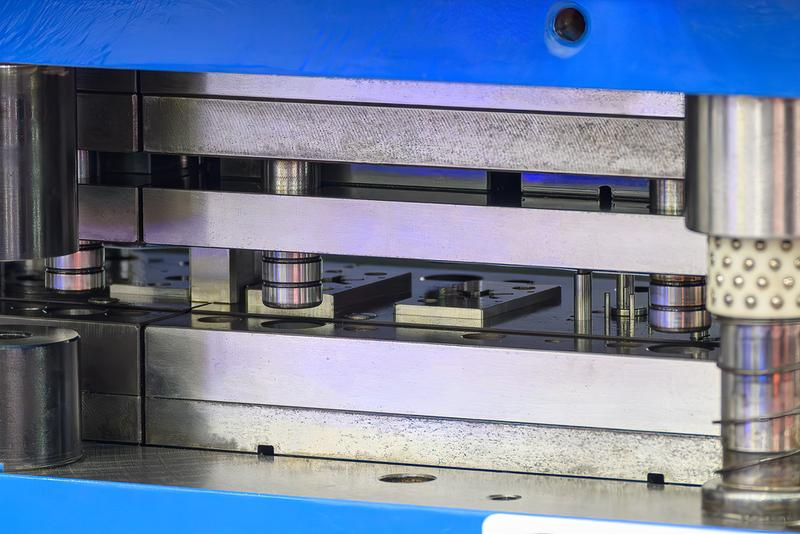
1. Abnormal Convex Die Wear: Causes and Countermeasures
1.1 Insufficient die clearance—typically, total die clearance should be 15-25% of material thickness.
1.2 Poor alignment between convex and concave dies, with precision issues in die bases, guide components, or turret inserts causing disrupted part ejection.
1.3 Excessive die temperature resulting from continuous, uninterrupted production causing punch overheating.
1.4 Improper die sharpening methods leading to annealing and accelerated wear.
1.5 Uneven cutting forces during step punching, corner cutting, or shearing operations causing furniture hardware components to exert lateral forces that tilt the punch toward one side. This reduces clearance on that side, severely increasing wear. If machine installation precision is inadequate, punch misalignment can destroy both convex and concave dies.
2. Comprehensive Solutions for Die Material Retention Issues
Material retention causes waste rebounding, influenced by several factors:
- Sharpness of die cutting edges—larger edge radii increase likelihood of material rebound
- Die insertion depth—fixed machine upper positions with small die measurements increase waste rebound risk
- Appropriate die clearance—improper clearance easily causes material retention
- Excessive oil on workpiece surfaces
- Damaged spring components
Prevention methods include:
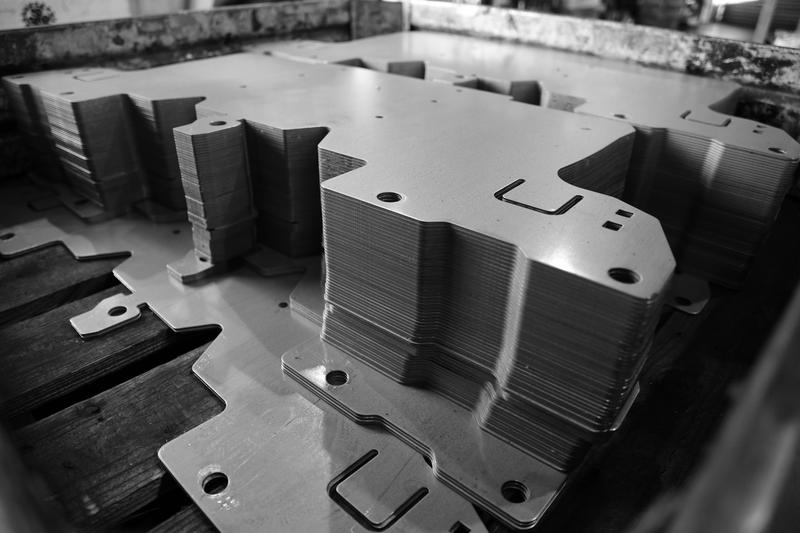
- Using specialized anti-retention concave dies for furniture hardware stamping
- Regular sharpening to maintain edge sharpness with demagnetization treatment
- Increasing concave die clearance
- Replacing flat-edge dies with inclined-edge designs
- Installing ejection mechanisms
- Appropriately increasing die insertion depth
- Inspecting spring or unloading sleeve wear conditions
3. Die Alignment Assurance Systems
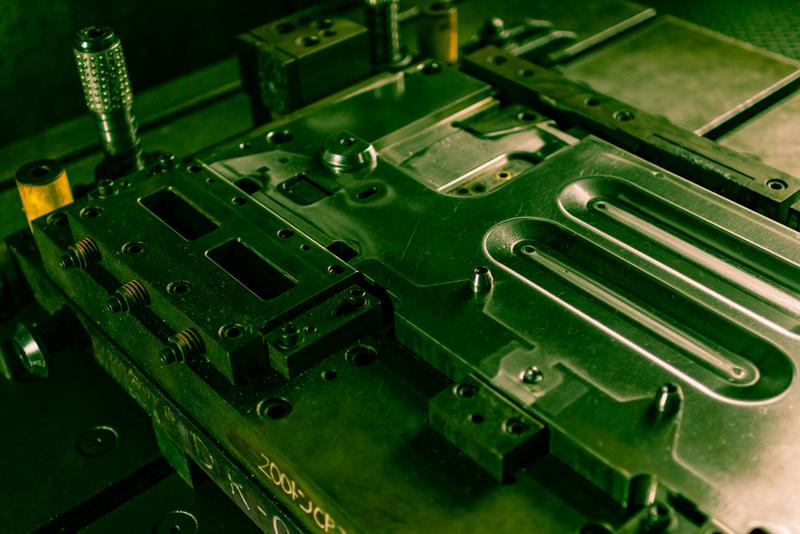
Furniture hardware stamping dies often develop uneven wear patterns around punch cores, with some sections showing larger scratches and accelerated wear. This is particularly noticeable in narrow rectangular dies, caused by:
- Insufficient turret design or machining precision, especially poor alignment between upper and lower mounting positions
- Inadequate die design or production precision
- Insufficient guide sleeve precision for convex dies
- Inappropriate die clearance selection
- Poor alignment due to long-term wear of mounting seats or guide sleeves
To prevent uneven die wear:
- Regularly maintain alignment core rods and check/adjust turret and mounting seat alignment
- Promptly replace guide sleeves and select appropriate clearance for convex and concave dies
- Utilize full-guide travel dies for furniture hardware stamping
4. Engineering Controls for Special Forming Dies

To fulfill customer orders and meet furniture hardware production requirements, forming or special dies are frequently needed. These special forming dies can significantly improve production output but typically cost 4-5 times more than standard dies. To avoid costly mistakes:
- Verify die orientation during installation, ensuring consistent direction of convex and concave components
- Accurately adjust stamping depth according to requirements, limiting adjustments to 0.15mm
- Operate at lower cutting speeds for furniture hardware stamping
- Use flat materials without deformation or warping
- Position forming operations away from clamps
- Avoid downward forming operations with special dies
- Follow proper operation sequence: standard die stamping first, forming dies last
5. Preventive Maintenance for Spring Systems
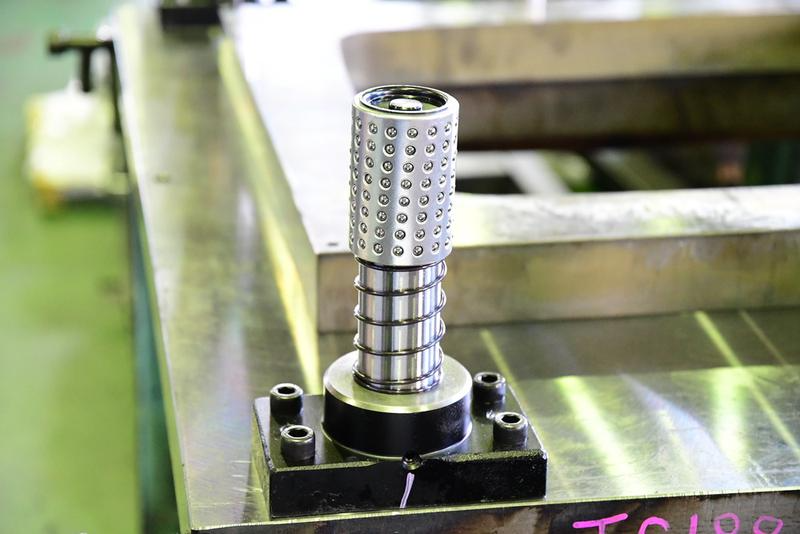
A commonly overlooked issue in punch press die operations is spring lifespan in furniture hardware component production. Die springs require regular maintenance or replacement, yet many Chinese factories maintain equipment and dies while neglecting spring maintenance—some users never replace springs for years.
When the same station or die frequently fails or retains material without apparent cause, replacing die springs often completely resolves the issue. Different punch press equipment and dies require different spring systems. Improper maintenance easily leads to material retention and potential damage to dies or guide sleeves, causing unnecessary losses in furniture hardware stamping operations.
Related News