Key Surface Treatment Processes for Metal Stamping Components in Furniture Hardware Manufacturing
Release time:
2025-04-25
In the metal stamping and furniture hardware manufacturing industry, surface treatment represents a critical production stage. This process not only enhances aesthetic appeal but directly determines corrosion resistance, wear resistance, and overall service life of precision metal components. Improper treatment can lead to premature oxidation, rust formation, or excessive wear of custom metal fittings, significantly increasing production costs and reducing customer satisfaction. What are the essential considerations for surface treatment in metal stamping processes? Let's explore how to elevate your sofa leg hardware and other custom fittings to premium quality standards!
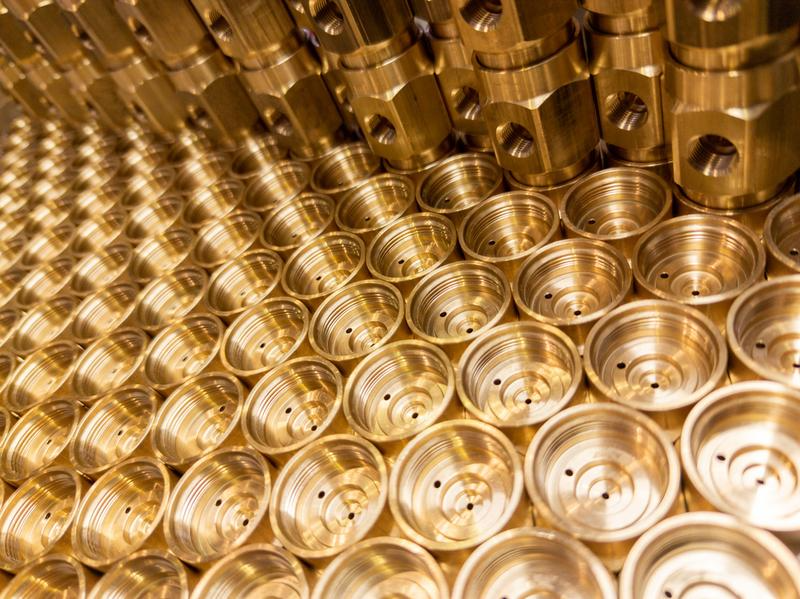
The Necessity of Surface Treatment for Metal Stamping Components
Industry newcomers often ask: "Since metal stamping creates inherently durable components, why invest in additional surface treatments?" The reality is that all metal materials—regardless of initial durability—gradually deteriorate when exposed to environmental factors such as atmospheric moisture, chemical contaminants, and mechanical friction. Scientifically optimized surface treatments not only enhance corrosion and rust resistance but also improve hardness, surface finish, and overall performance of custom metal fittings.
Technical Note: Different applications of metal stamping require specific surface treatment solutions. For example, outdoor furniture hardware demands superior corrosion resistance, while precision components for smart furniture mechanisms require ultra-smooth surfaces with optimized friction coefficients.
Leading Surface Treatment Technologies for Metal Stamping Components in Furniture Hardware
The furniture hardware industry currently employs several advanced surface treatment methodologies for metal stamping components, including electroplating, powder coating, anodizing, polishing, and heat treatment. Each technique offers unique benefits for specific applications. Let's examine these processes to provide comprehensive insight into selecting the optimal treatment for your custom sofa leg hardware and other metal fittings.
1. Electroplating: Premium Protection for Metal Stamping Components
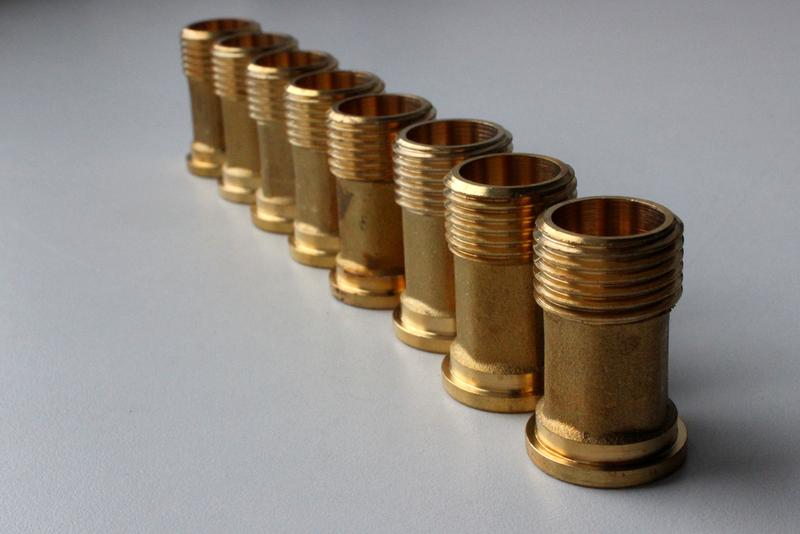
Electroplating represents the most widely implemented surface treatment in precision metal stamping. This electrochemical process deposits a thin layer of protective metal—such as nickel, zinc, or chromium—onto the substrate. This treatment significantly enhances oxidation resistance while simultaneously improving wear resistance and aesthetic appeal of custom metal fittings.
Industry Applications: Furniture hardware components, power tool accessories, and precision mechanical parts frequently undergo electroplating to maximize durability. For instance, premium sofa leg hardware typically receives nickel-chrome plating, ensuring long-term luster retention and superior rust prevention after installation.
Technical Considerations:
- Select appropriate electroplating materials to prevent adhesion failures and subsequent delamination
- Ensure thorough pre-cleaning protocols, as contaminant residue significantly compromises electroplating integrity
- Adhere to environmental regulations governing heavy metal usage (particularly chromium), maintaining compliance with current industry standards
2. Powder Coating: Combining Aesthetic Versatility with Functional Protection
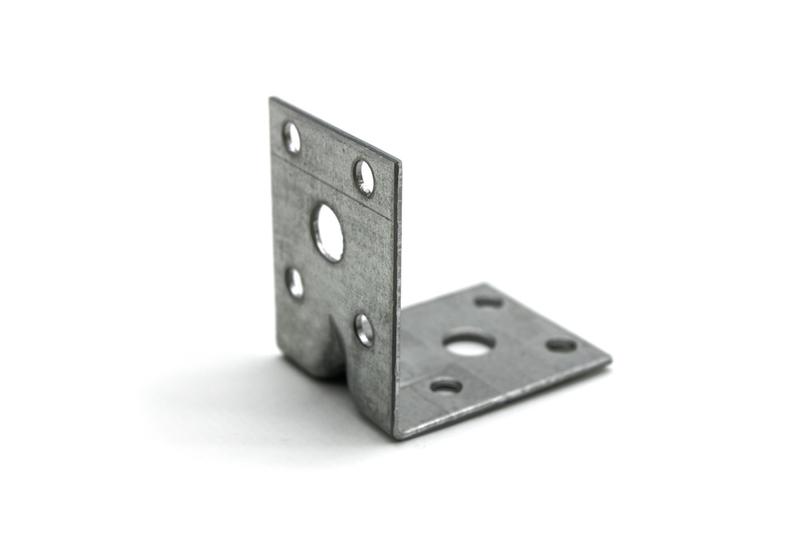
For manufacturers seeking both protective functionality and decorative versatility in their metal stamping components, powder coating offers an ideal solution. This environmentally sustainable process utilizes electrostatic attraction to apply polymer powder evenly across the component surface before high-temperature curing creates a durable protective film. This technique effectively eliminates the adhesion issues common with conventional liquid coatings while providing substantial corrosion protection.
Industry Applications: Custom sofa leg hardware, coffee table supports, dining table frames, angle brackets, hinges, and sliding mechanisms frequently utilize electrostatic powder coating technology. This treatment delivers exceptional weather resistance while maintaining vibrant color stability. Industrial equipment manufacturers also favor this process for its ability to create uniform protective layers of customizable thickness, substantially extending component service life.
Manufacturing Tip: When implementing powder coating for precision metal stamping components, careful thickness control is essential—excessive coating thickness compromises assembly tolerance, while insufficient application fails to deliver optimal protection.
3. Anodizing: Enhancing Aluminum Alloy Performance in Metal Stamping Applications
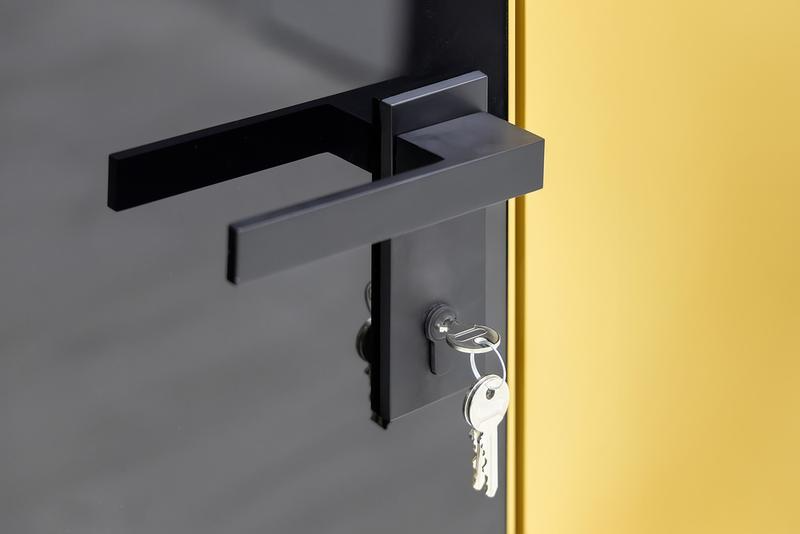
Anodizing primarily serves aluminum and aluminum alloy stamped components by fundamentally transforming the metal's surface structure to create a dense, exceptionally hard oxide film. This treatment dramatically improves corrosion and wear resistance while allowing for customized coloration and pattern application—making it ideal for decorative furniture hardware components requiring performance longevity.
Industry Applications: Many commonly used custom fittings including door handles, aluminum alloy hinges, and support brackets implement anodizing treatments. For example, precisely engineered drawer slides and height adjustment mechanisms deliver their characteristic smooth operation and scratch resistance specifically because of advanced anodizing processes. Similarly, aluminum window frames and decorative trim components resist environmental degradation while enhancing aesthetic appeal through precisely controlled anodizing.
Technical Advantages: Anodizing delivers superior hardness enhancement with unmatched color customization flexibility. However, this specialized process applies exclusively to aluminum-containing materials—steel and other non-aluminum metal stamping components require alternative treatment methods.
4. Polishing: Elevating Surface Quality and Precision in Metal Stamped Fittings
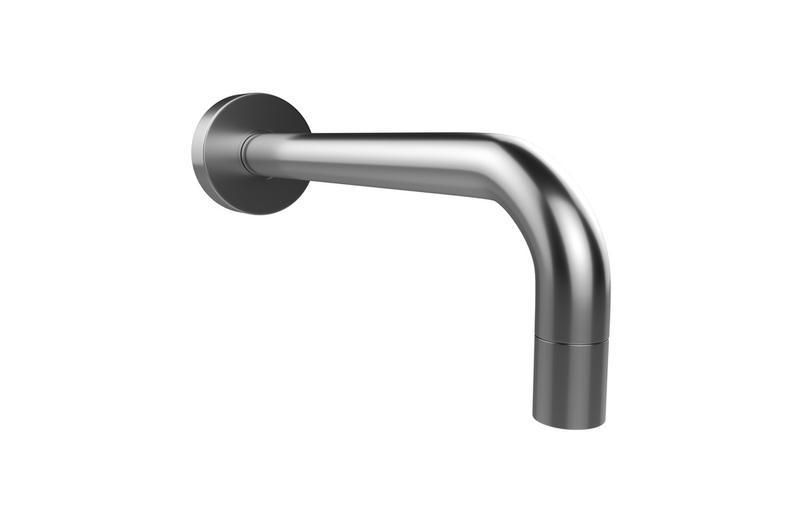
When premium metal stamping components require mirror-finish quality and superior tactile experience, polishing becomes essential. This precision process mechanically removes microscopic surface irregularities, creating exceptionally smooth surfaces. Often combined with complementary techniques such as mirror buffing or directional finishing for stainless steel components, polishing reduces friction, enhances assembly precision, and delivers the premium aesthetic essential for high-end furniture hardware components.
Industry Applications: The polishing process proves invaluable for various metal stamping applications: cabinet hinges benefit from burr removal and smoother articulation; drawer slides experience reduced friction and extended operational life; door locks and catches gain enhanced corrosion resistance; and custom sofa leg hardware benefits from reduced panel material abrasion. This versatile process applies to zinc alloy, stainless steel, and brass components, eliminating surface imperfections through precision mechanical or chemical processes to achieve optimal smoothness and corrosion resistance.
Design Consideration: While polishing dramatically enhances both tactile and visual qualities, certain high-friction applications may actually experience increased scratch vulnerability with highly polished surfaces. Comprehensive application analysis during the design phase ensures appropriate surface finish specification for each custom metal fitting.
Selecting the Optimal Surface Treatment for Your Metal Stamping Components
When navigating the diverse array of surface treatment options for precision metal stamping components, manufacturers should base decisions on three critical factors: operational environment, budget constraints, and performance requirements. For applications prioritizing corrosion resistance, electroplating and powder coating offer superior protection; when seeking customized aesthetics with exceptional durability, anodizing presents the optimal solution; and for intricate components requiring premium tactile quality, combining polishing with appropriate heat treatment delivers unmatched performance. By strategically selecting the right surface treatment technology, manufacturers can optimize their custom sofa leg hardware and other metal stamping components for both performance and longevity.
Related News