Metal Stamping Die Design: Optimal Clearance Selection for Quality Hardware Components
Release time:
2025-04-30
Understanding Die Clearance in Metal Stamping for Custom Fittings and Sofa Leg Hardware
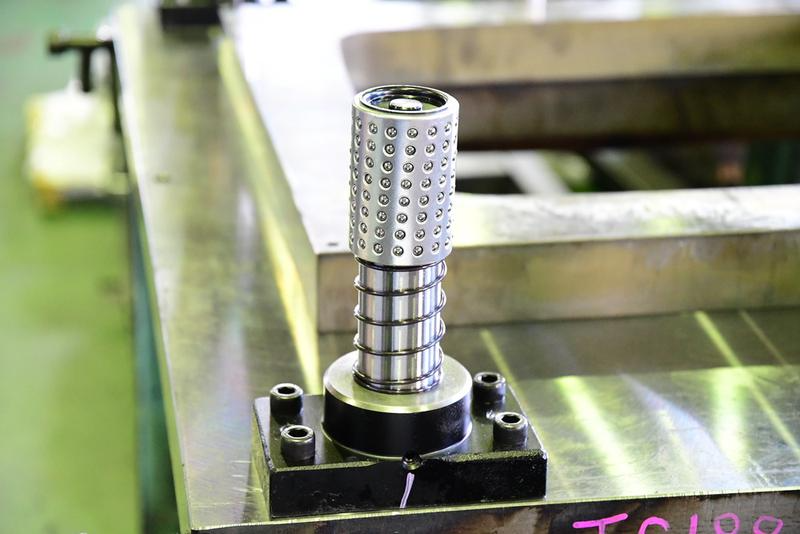
In stamping die manufacturing, determining the appropriate clearance involves complex engineering considerations. The clearance value directly impacts die precision, tool lifespan, and production costs (machining expenses) for metal stamped components including sofa leg hardware and custom metal fittings.
Among all clearance types, cutting clearance is the most adaptable yet challenging to perfect. Material properties, sheet thickness, product cross-section quality requirements, and dimensional precision all influence the optimal clearance value for precision metal stamping operations.
Definition of Cutting Clearance in Metal Stamping Dies
Cutting clearance refers to the space between the convex and concave dies (punch and die cutting edge) used for stamping materials. The formula is: Z = D - d
Note: Z—cutting clearance, D—die edge dimension, d—punch dimension
There's a distinction between single-sided and double-sided clearance, typically defined according to optimal cutting clearance standards for custom metal hardware production.
Relationship Between Stamping Quality and Cutting Clearance
1. Cutting Clearance and Cross-Section Quality

Normal clearance effects: Upper and lower fractures align, large burnished band, minimal die roll, burrs, and taper, with smooth surface finish—ideal for precision sofa leg hardware components.
Excessive clearance effects: Upper and lower fractures misalign, increased tearing, rough cross-section, small burnished band, significant die roll, burrs, and taper.
Insufficient clearance effects: Upper and lower fractures misalign, secondary shearing occurs, creating a second burnished band with large burrs—problematic for high-quality metal fittings.
Uneven clearance effects: The side with smaller clearance exhibits characteristics of insufficient clearance, while the side with larger clearance shows excessive clearance traits.
2. Cutting Clearance and Dimensional Accuracy
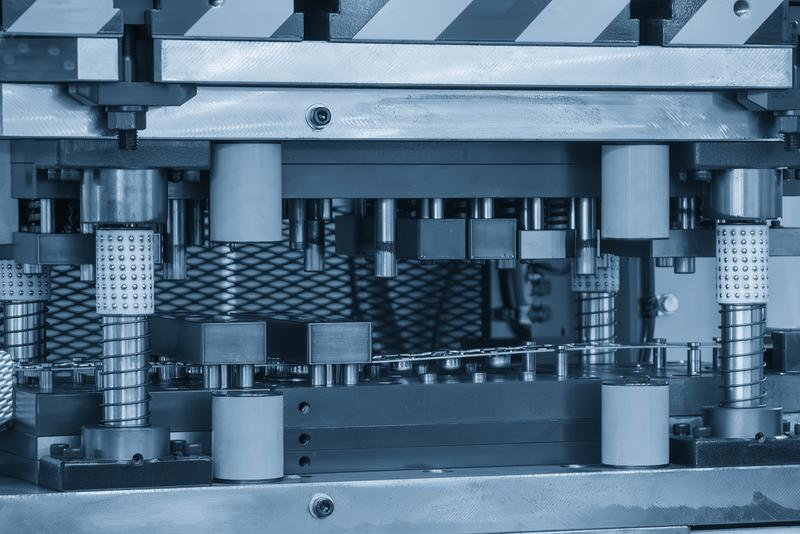
Increased clearance, when punching holes: Metal experiences greater inward pulling, and elastic recovery causes workpiece dimensions to increase (hole size).
Increased clearance, when blanking: Metal stretching increases, and elastic recovery reduces workpiece dimensions (stamped part size).
Reduced clearance, when punching holes: Greater metal compression reduces hole size.
Reduced clearance, when blanking: Increased internal pressure enlarges workpiece dimensions.
3. Cutting Clearance and Stamping Force
When cutting clearance decreases, material deformation and fracturing become more difficult, gradually increasing stamping force. When clearance increases, material deformation and fracturing become easier, gradually reducing stamping force required for metal stamping operations.
As cutting clearance affects stamping force, stripping force follows similar patterns. When cutting clearance reaches 15%-20%T, stripping force becomes negligible in custom hardware manufacturing.
4. Cutting Clearance and Die Service Life
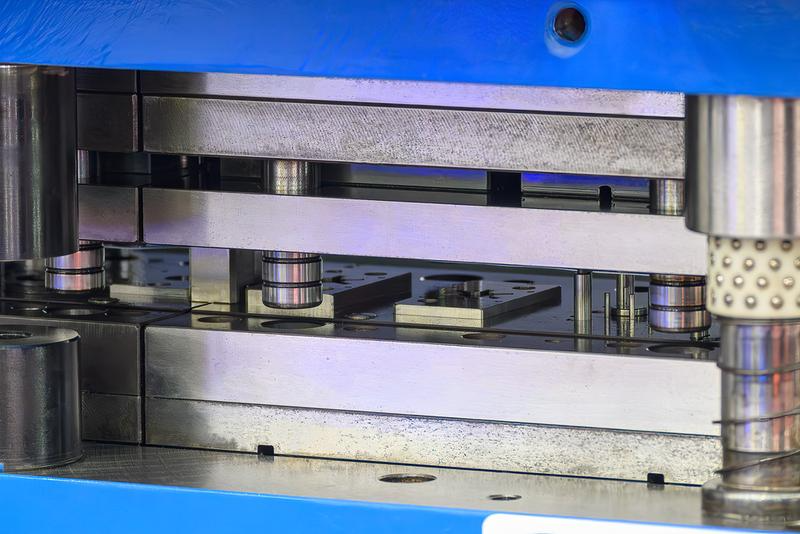
Cutting clearance size affects friction between material, die edge, and punch. Smaller clearance increases friction, reducing punch and die edge service life, while larger clearance extends service life for tools used in manufacturing sofa leg hardware and other metal fittings.
5. Defining "Optimal Cutting Clearance" for Metal Stamping
Optimal cutting clearance involves maximizing clearance while ensuring dimensional accuracy and cross-section quality to meet all die performance requirements for precision metal components.
This clearance represents a range of values that satisfy all requirements. However, selection should follow these priority conditions:
- When product cross-section quality is not critical, choose larger cutting clearance to achieve longer die service life and lower tonnage requirements for metal stamping operations.
- When product cross-section quality and dimensional accuracy requirements are high (as in precision sofa leg hardware and custom metal fittings), select smaller cutting clearance values.
Related News