Automated Sofa Leg Hardware Manufacturing: The Future of Stamping Technology
Release time:
2025-04-17
The Current State and Future of Sofa Leg Hardware Stamping Factories in China
The number of sofa leg hardware stamping factories in China has yet to be officially counted, as they vary significantly in size. Large factories primarily utilize automated stamping machines, while small and medium-sized operations still largely rely on semi-automatic and manual production methods. Large furniture hardware stamping factories emphasize precision and mass production, resulting in sofa leg hardware components that maintain quality standards while being produced rapidly. These larger manufacturers typically have established brand recognition, which justifies their somewhat higher unit prices for furniture hardware accessories.
For the furniture hardware stamping industry, each year and each quarter essentially marks a fresh start. This is because furniture manufacturers' requirements change annually, with new sofa, bed, and coffee table designs requiring different hardware components. Of course, there remains consistent demand for existing products, with popular hardware items continuously favored by distributors and furniture manufacturers.
Small to medium-sized factories still employ traditional stamping production methods that depend heavily on manual operations. Frequent mold changes and adjustments significantly increase both production and time costs. From an industrial automation reform perspective, processes that are simple and highly repetitive are easiest to automate—characteristics that align perfectly with the stamping industry. The benefits of such automation are particularly evident in the stamping sector, making the replacement of human labor with machines an irreversible trend.
Advantages of Machine Automation
01
Stamping robots and mechanical arms offer continuous, stable operation advantages that overcome the limitations of manual operations. They don't suffer from fatigue, are simple to operate, significantly reduce the risk of safety accidents caused by human error, and improve both production efficiency and product quality.
02
Stamping operations typically take place in poor environments—narrow, disorganized spaces with extreme weather conditions (such as very high or low temperatures) and prolonged noise exposure, which can easily lead to safety incidents. Stamping robots and mechanical arms demonstrate strong adaptability and, once programmed, can reduce accident risks significantly.
03
Robotic processing delivers high precision, ensuring production quality while reducing defect rates. These systems can replace certain human labor, particularly repetitive and tedious tasks, thereby reducing labor costs.
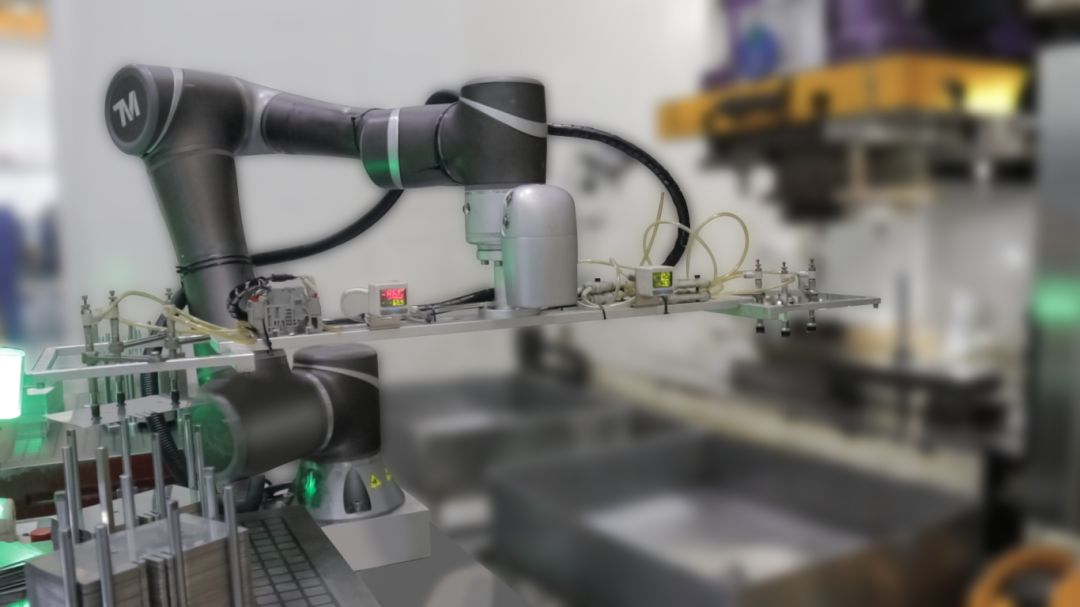
Stamping robots must meet requirements for heavy loads, precise trajectories, and reliable operation while adapting to frequent starts and stops and handling workpieces with large operational ranges. Automated stamping robotic equipment has emerged to meet these needs, utilizing collaborative robots for automatic loading and unloading, precise handling, reduced personnel strain, and quality improvement. When combined with CCD detection for product positioning, this technology prevents mold damage and achieves efficient, high-quality, cost-effective production.
Equipment Advantages
Rapid Mold Changes and Simple Program Switching
The stamping industry faces challenges of high-intensity, highly repetitive work with obvious labor cost and efficiency bottlenecks. Stamping robot equipment offers advantages in rapid mold changing and easy program switching, greatly reducing downtime and complexity. Quick adjustments for different products significantly improve production efficiency and flexibility, easily meeting diverse market demands.
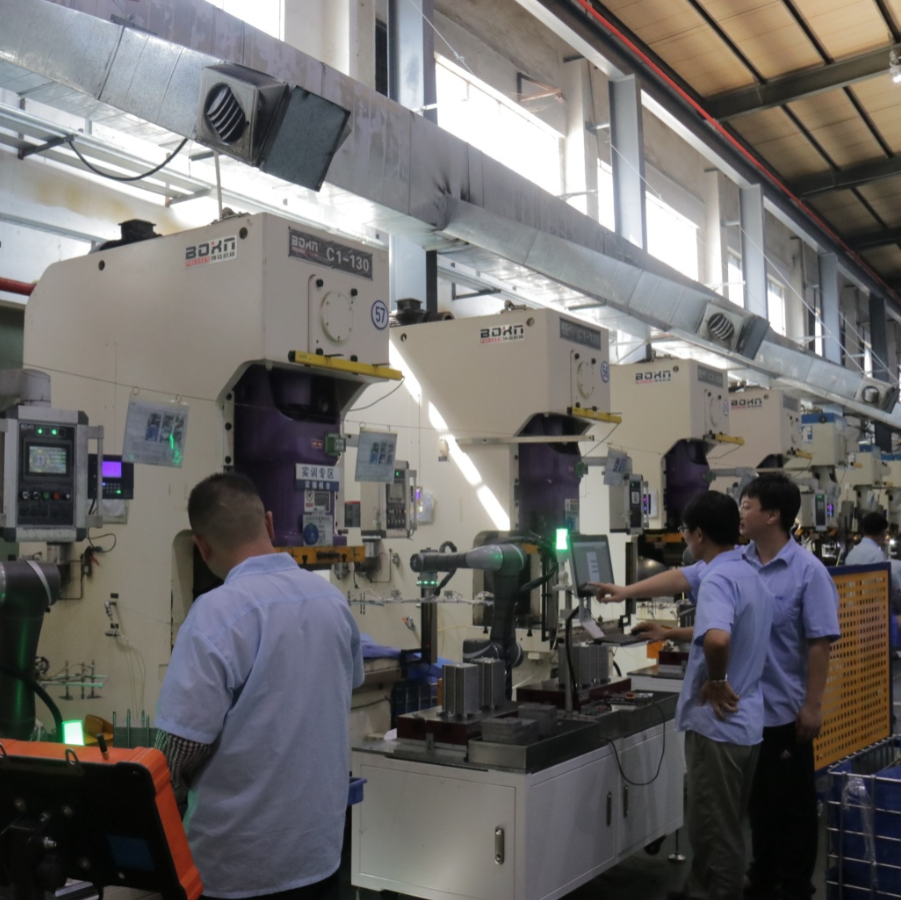
Dual-Position Feeding Area and Material Storage Advantages
The stamping industry often faces unstable material supply issues that affect production continuity. Automated stamping robot equipment features a dual-position feeding area design that enables material replenishment without stopping production. Combined with large-capacity material storage, this ensures continuous, stable material supply, reducing the risk of production interruptions due to material shortages and improving overall production efficiency.
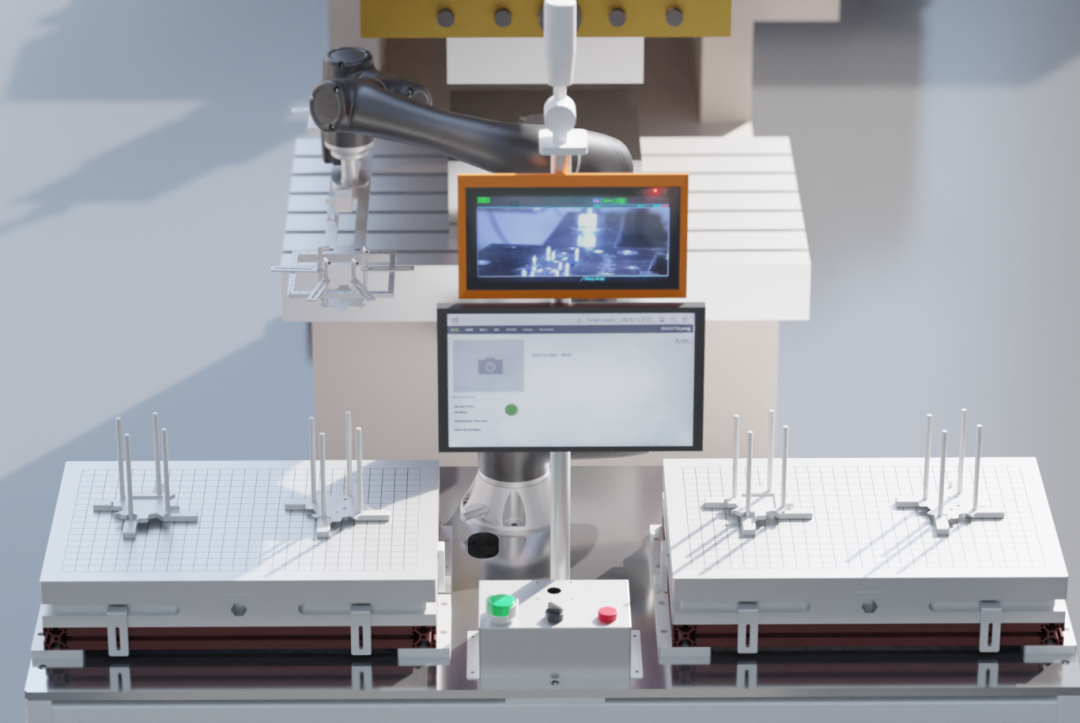
Collaborative Robots with High Safety Performance
The stamping industry faces worker safety challenges due to high-intensity, high-risk operations. Stamping equipment's collaborative robot technology offers excellent safety performance, reducing accident risks and providing worker protection while enhancing overall production safety.
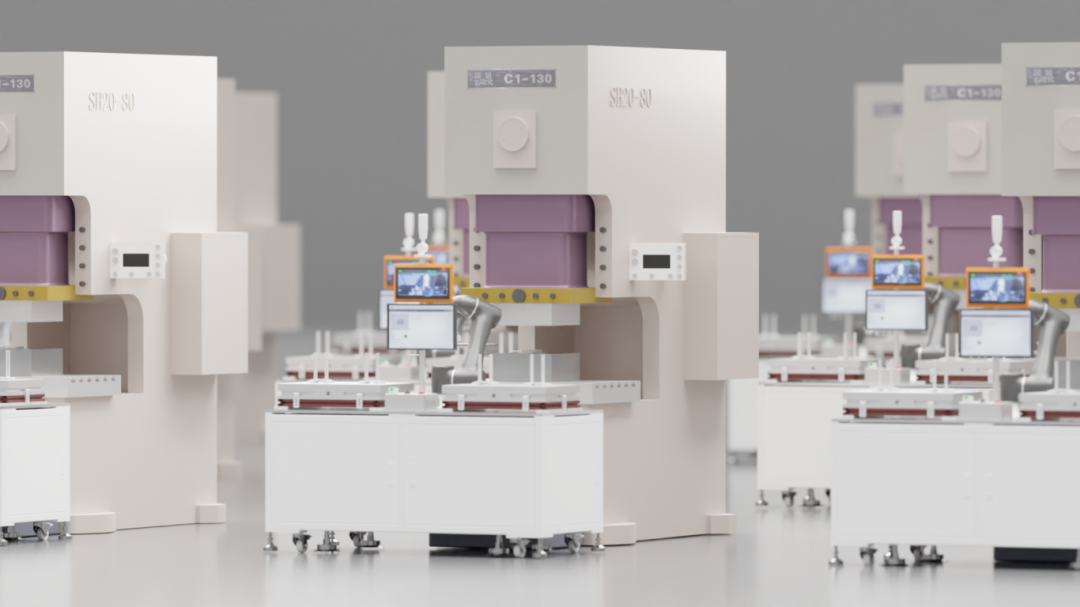
User-Friendly Programming System with Strong Product Compatibility
Equipped with an easy-to-operate programming system that makes programming simple and fast, these systems offer strong compatibility supporting various products. Whether dealing with simple or complex stamping workpieces, this system allows for easy completion, significantly improving production efficiency, precision, and safety. Compared to traditional manual stamping methods, it effectively frees up human resources and helps enterprises enhance overall production benefits.
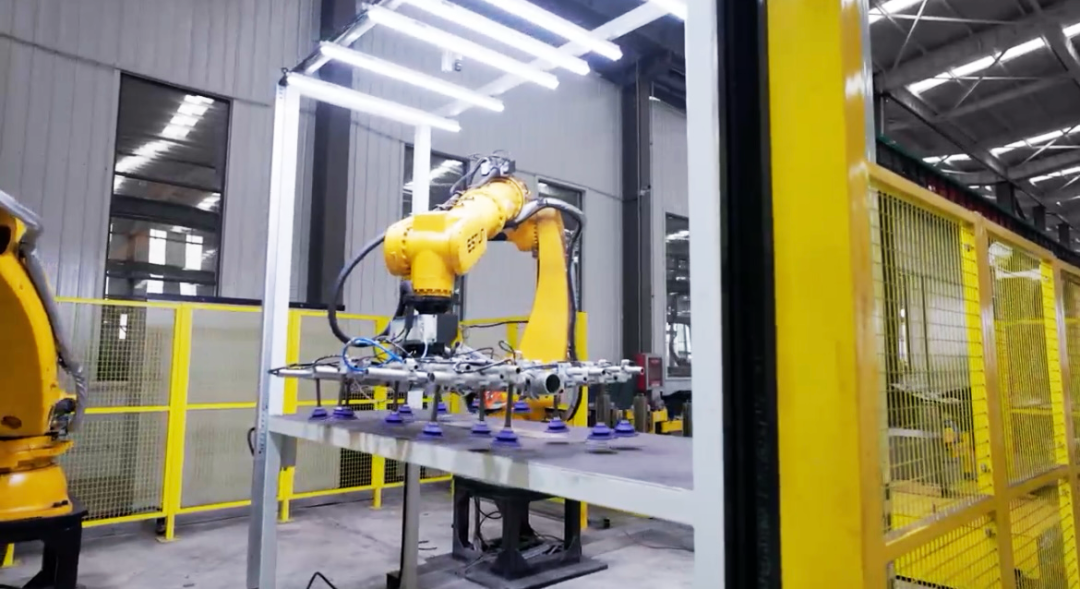
CCD Detection Positioning to Prevent Mold Damage
Molds are central to stamping production but have short lifespans and high maintenance costs. Many molds fail to reach their expected lifespan in actual use, experiencing serious wear and damage that leads to frequent replacements, severely affecting production efficiency and increasing manufacturing costs. Stamping robot equipment, with advanced CCD vision functionality, monitors product positioning in real-time and processes abnormal alarms while reducing downtime. This effectively prevents mold collisions and damage, precisely avoiding mold damage caused by unexpected abnormal stamping, providing effective protection for stamping molds, and reducing mold repair costs for enterprises.
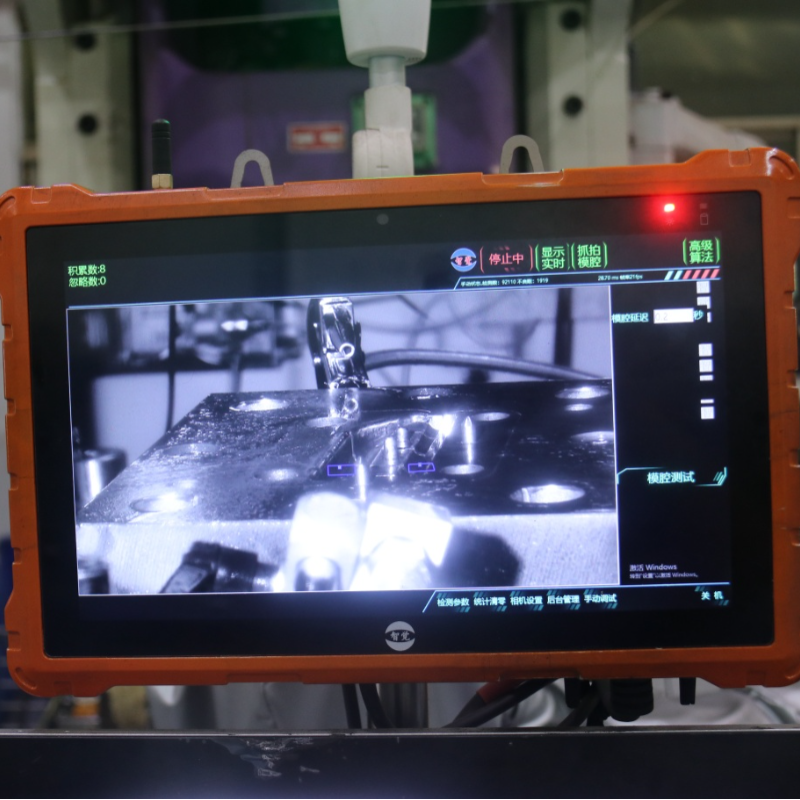
Flexible Suction Cup Structure for Multi-Product Compatibility
Using a unique flexible suction cup structure with distinctive design, these systems flexibly adapt to multiple products, achieving efficient and precise grabbing and positioning of products with various shapes and sizes. This reduces downtime and production costs caused by incompatible suction cups, meeting enterprises' diversified production needs.
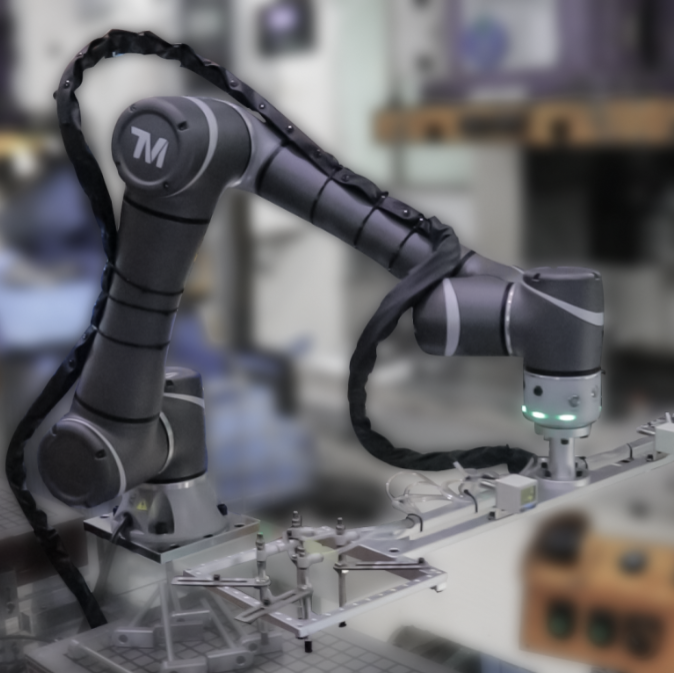
One Operator Managing Multiple Machines
CCD visual inspection replaces manual monitoring, enabling one person to oversee multiple pieces of equipment while improving production efficiency and effectively reducing labor costs. Operators can simultaneously monitor multiple machines, achieving quick response and efficient management, reducing workload, improving work comfort, and ensuring product quality and production stability. An intelligent fault diagnosis system monitors in real-time, quickly resolving problems and reducing downtime.
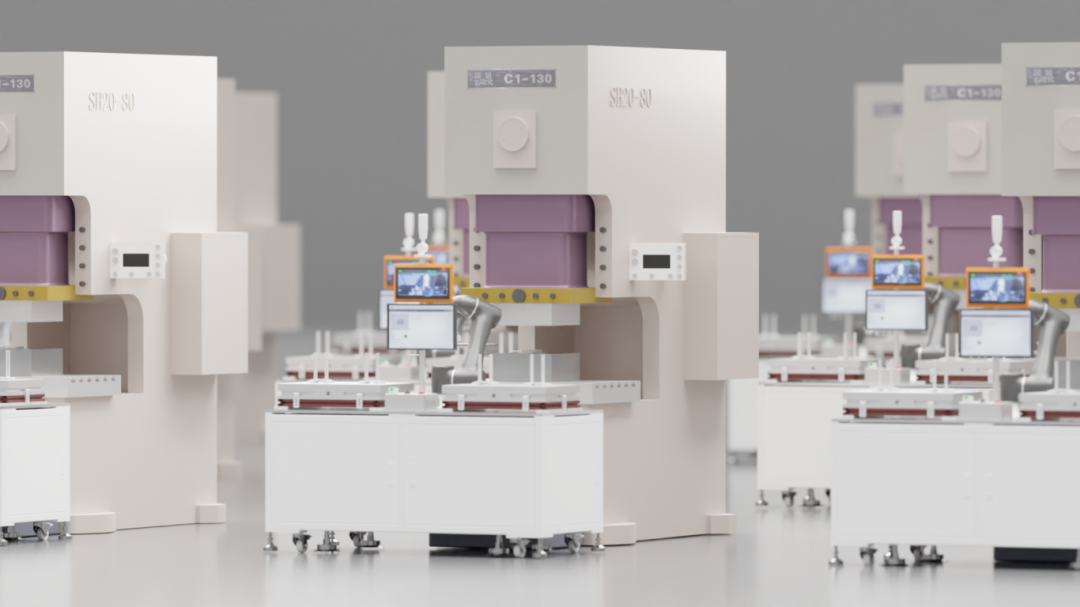
Meeting Small-Batch, Diverse Production Requirements
Traditional stamping production models struggle to meet multi-variety, small-batch production demands and fail to satisfy market requirements for small-volume, diverse processes. However, automated stamping robot equipment shows significant advantages, with single fixture sets applicable to multiple products and quick changeovers that can meet stamping process requirements for small quantities and diverse varieties, greatly improving production efficiency and flexibility.
Targeting the pain points of traditional stamping production lines, automation provides targeted solutions using high-performance, stable robotic equipment that leads development trends in the stamping industry. This resolves numerous issues in traditional stamping production lines, improving production efficiency, reducing costs, decreasing workplace accidents, and injecting new vitality into enterprises' sustainable development.
Related News