How Factories Control Surface Scratches on Sofa Leg Stamping Parts
Release time:
2025-04-03
Surface scratches on sofa leg stamping parts represent a common quality defect that stamping manufacturers' technical personnel frequently encounter during production. This issue is widespread across major stamping production factories. These product quality defects not only reduce production stability and efficiency but also lead to increased scrap rates of mechanical parts. Additionally, they cause more severe wear on molds, reducing die life and stamping precision while increasing the frequency of die repairs and production downtime.
The Nature of Surface Scratching
The essence of surface scratching is due to local adhesion (binding) between the sofa leg workpiece and the mold surface. There are multiple methods to improve this issue, with the basic principle being to change the nature of the friction pair between the mold and the processed part, replacing it with materials that are less prone to adhesion. After the mold enters the debugging phase at the production site, the following methods are generally used to improve surface scratching:
- Changing mold materials and increasing mold hardness
- Treating the mold surface through processes such as hard chrome plating, PVD, and TD
- Coating the mold cavity with nano-coatings, such as RNT technology
- Adding a layer of other substances between the mold and the processed part to separate them (such as applying lubricants, special lubricants, or adding PVC-type materials)
- Using self-lubricating coated steel plates
Mold Material Selection
In terms of mold materials, tool steels like SKD11 and CR12MOV are widely recognized as wear-resistant and anti-binding materials. After heat treatment, these materials can reach a hardness of approximately HRC58-63 on the Rockwell hardness scale. These materials can be adopted when the mold is not large and the part shape is relatively simple. However, such materials are difficult to process after heat treatment, have high brittleness, are prone to cracking, are costly, have size limitations, and undergo significant deformation after heat treatment, requiring extensive post-treatment fitting work.
For sofa leg hardware parts with complex shapes, and when customers require high-strength steel plates, the overall performance requirements for molds are higher. Some automotive stamping operations typically adopt a modular insert structure, with surface treatment processes for the inserts including TD, hard chrome plating, nitriding, PVD, and others.
TD Treatment Process
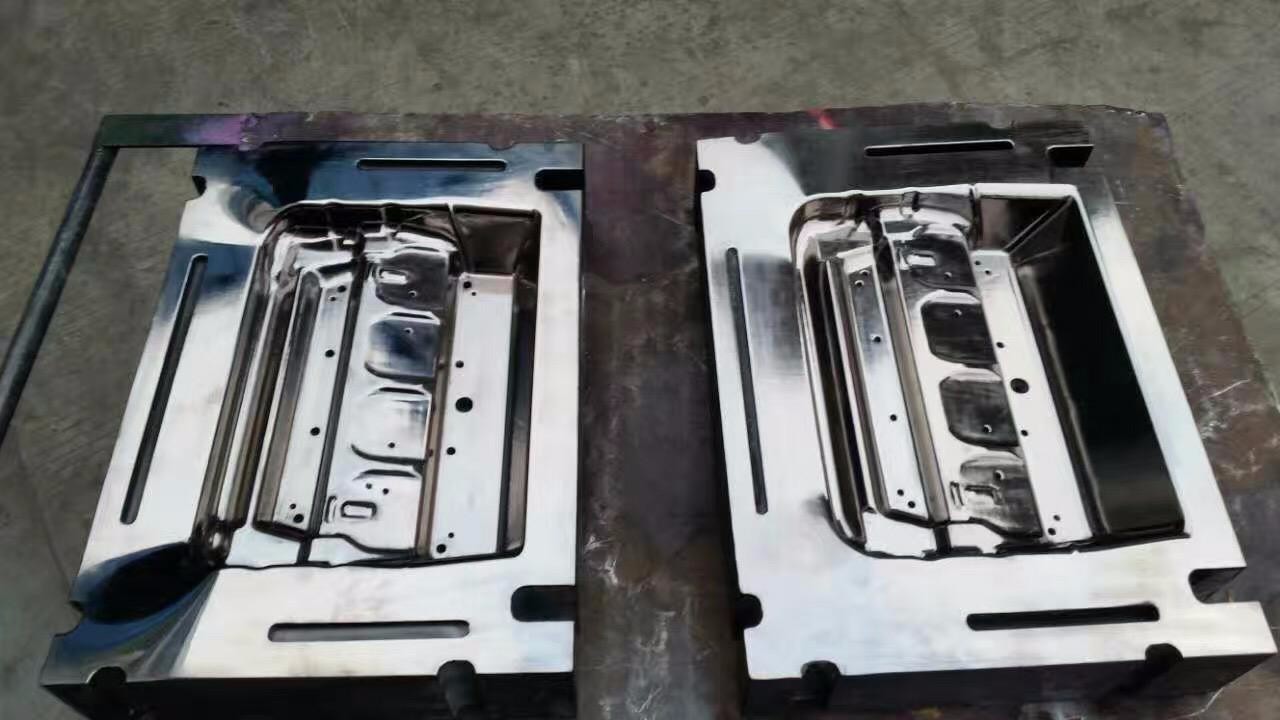
TD treatment is an abbreviation for Thermal Diffusion Carbide Coating. This technology was first developed and patented by Toyota Central Research Institute in the 1970s, also known as the Toyota Diffusion Process or TD Process. In China, it's also called molten salt metal infiltration. Regardless of the name, the principle involves placing workpieces in a molten borax mixture, forming a metal carbide coating on the workpiece surface through high-temperature diffusion. TD treatment is commonly used in high-strength applications such as automotive parts, with relatively limited relevance to furniture hardware like sofa legs.
The main characteristics of TD coating include high hardness (approximately HV3000), excellent wear resistance, scratch resistance, and corrosion resistance, with a service life of around 100,000 units. However, TD coating has high requirements for mold materials and, as a high-temperature treatment, the thermal stress, phase transformation stress, and specific volume changes can easily cause mold deformation or even cracking during the heat treatment process. Repaired molds will typically develop cracks at the weld. TD coating treatment has high requirements for the processing quality and shape of the mold. Additionally, molds are difficult to process after TD coating treatment, making it challenging to meet design changes and mold adjustment needs. For molds that have undergone other surface treatments, the original surface treatment must be thoroughly removed; otherwise, it will affect the TD coating surface quality. Furthermore, TD coating technology generally shows reduced service life after 3-4 treatments. If the sofa leg uses thick steel plate (≥1.5mm) or requires high wear resistance, TD coating can be considered; however, furniture stamping generally has lower hardness requirements, so TD might be "performance excessive" and costly.
PVD Coating Technology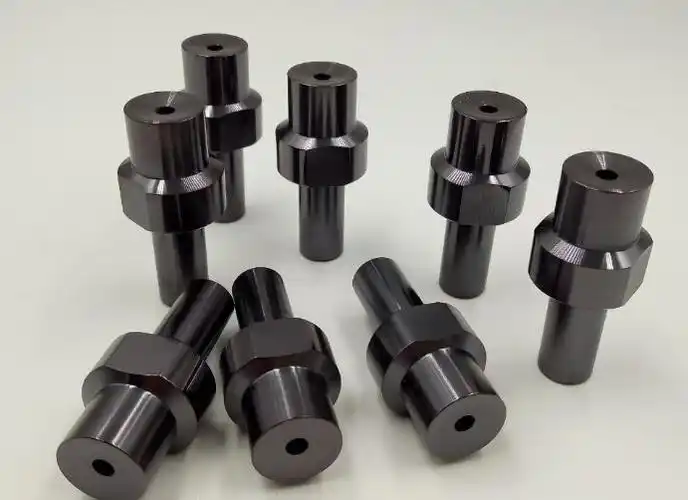
PVD (Physical Vapor Deposition) refers to surface coatings manufactured using physical vapor deposition methods. It offers good scratch resistance, with coating hardness reaching HV2000-3000 or even higher, providing excellent wear resistance. Its advantages include lower processing temperature, minimal workpiece deformation, and the ability to be treated multiple times without affecting service life. However, its coating has relatively poor adhesion to the substrate and can easily peel off when used on drawing dies and molds with high forming pressure, failing to deliver its anti-scratch and wear-resistant effects. If the sofa leg is made of thin plates (below 1mm) or requires high surface finish, PVD offers good cost-effectiveness; however, since the coating adhesion is relatively weak, it's not suitable for high-impact stamping.
Treatment for Large Panel Dies
Panel dies are generally larger in size. If a modular insert structure is adopted, scratching may occur at the joints, so integral structures are often used, typically made of ductile iron or other cast iron materials. After flame hardening of the forming and material transfer areas, hardness can reach approximately HRC50-55 on the Rockwell scale.
Surface treatment for integral panel dies mostly adopts hard chrome plating technology, but its surface hardening effect is limited, with surface hardness around 1000HV. Additionally, the hard chrome plating layer forms a mechanical bond with the mold substrate and can easily peel off under high forming pressure, losing its scratch resistance once detached. When the surface hardening layer wears out, scratches will reappear, with a service life generally around 50,000-100,000 units. If the sofa leg requires rust prevention or a bright surface (such as gold-plated appearance), hard chrome plating is an economical choice; however, its wear resistance is inferior to TD/PVD, and long-term stamping may require frequent repairing.
RNT Technology Applicatios
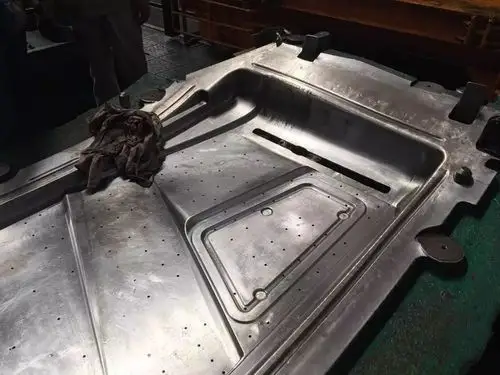
RNT is an emerging technology in recent years. Its working principle involves coating the mold cavity with RNT coating liquid and using pressure to diffuse nano molecules to form a nano-metal carbide coating on the mold surface. This process expands from inside to outside, with thickness and hardness increasing with the mold's working time. The coating thickness is between 0.1-1μm, with a hardness of HV1100-1600. Even when the mold bears a larger load, the coating doesn't peel off due to substrate plastic deformation. Its thickness and hardness increase from inside to outside with the mold's working time and number of coatings.
A single application of RNT coating generally guarantees 100-500 parts without scratching. However, this technology is not yet mature for severely scratched parts, parts that generate heat during production, and ultra-high-strength plates, and its usage cost is relatively high. RNT is commonly used in hardware stamping dies (such as stainless steel, wrought iron parts, etc.), which can significantly reduce the number of die repairs and extend die life. If the sofa leg is made of thin plates or low-strength materials (such as aluminum), RNT may offer better cost-effectiveness than TD/PVD.
Lubrication Solutions
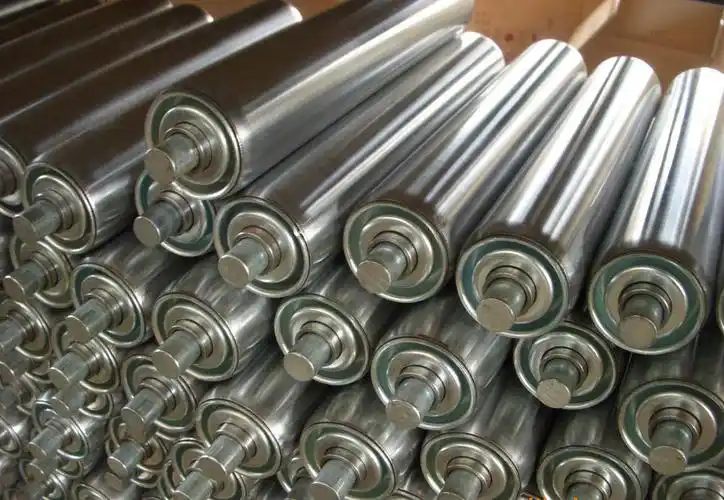
Using appropriate lubricants during the production process can effectively improve friction conditions and reduce scratching. Their main function is to separate contact pairs with a lubricating oil film. Oiling is generally done manually or using automated equipment at the line head. Additionally, using lubricants can effectively reduce hidden damage and cracking issues. However, using lubricants can make the environment dirty and slippery. To improve the impact of oiling on the working environment, steel enterprises like Baosteel, Wuhan Iron and Steel, and Maanshan Iron & Steel have developed self-lubricating steel plates in recent years. Self-lubricating coated steel plates offer excellent self-lubrication, corrosion resistance, fingerprint resistance, processing formability, and coating properties. They mainly involve rolling a layer of organic coating onto the steel plate, eliminating the need for additional lubricating oil during the stamping forming process. However, the usage cost is slightly higher, and it has not yet been widely adopted.
Conclusion
Due to the vast differences in forming loads and materials being formed, when deciding which measure or measures to adopt to solve workpiece scratching problems, one must consider not only the effectiveness of the solution but also the batch size of the product, the ease of implementation, economic factors, and other aspects before selecting the most appropriate method.
Related News